By Scott Sellers
COO Editorial Board
The last article about our 182RG rebuilding project (February 2022 issue) discussed propeller dynamic balancing and mentioned our plane’s problem of occasional rpm surging on the takeoff roll. It was my assumption that the surging issue was related to the prop governor, since it had 1,450 hours and 17 years of service since installation. This led to internal Cessna Owner Organization discussions on correct propeller operations related to rpm cycling pre-takeoff.
Governor Problem
Speeding down the runway with the throttle open when you can hear and feel the rpm surging at maybe 100 rpms gets your attention in a 300 hp Cessna 182 like ours. This would occur as often as every other takeoff.
Was the surging due to insufficient cycling of the propeller during runup, or other operator error I may have caused?
I asked this question of Mike Baird at Tiffin Aire prior to sending our McCauley DC290 D1 governor there for overhaul. Mike explained that the prop is slaved to the governor and that typically, for a governor with this length of service, the flyweight toes are worn, which results in rpm surging. See the picture at right (a page from Hartzell’s owner’s manual) and the picture at the top of Page 35 (taken during this governor’s disassembly).
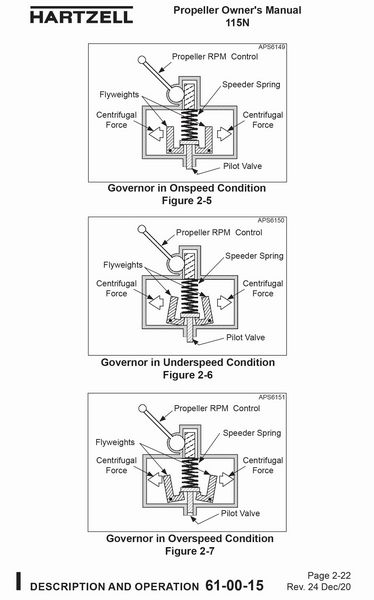
Upon disassembly of the governor, the folks at Tiffin were surprised to find the internal components were in like-new condition. The flyweights and other parts showed no signs of wear and thus were reused in the overhaul. This is very unusual indeed and kept the cost of the overhaul to a “mere” $1,250 (ouch). Tiffin’s technician Dennis Gase mentioned that they usually see governors come in for overhaul that require replacement of most of their internal components, making the cost of a new governor (about $2,100) the preferred option. Further searching online indicates overhauled governors of this model are available for $1,350, with the exchange of your old core.
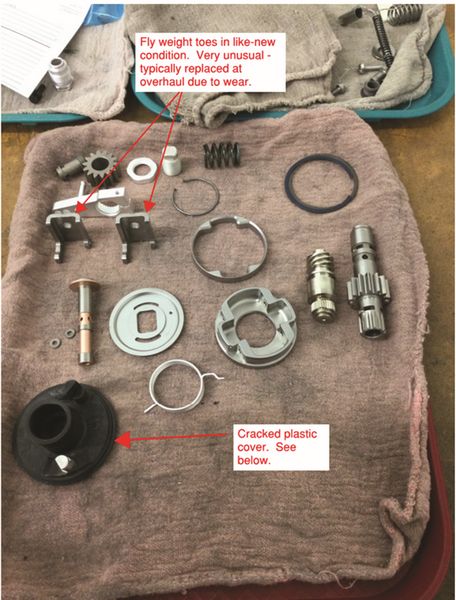
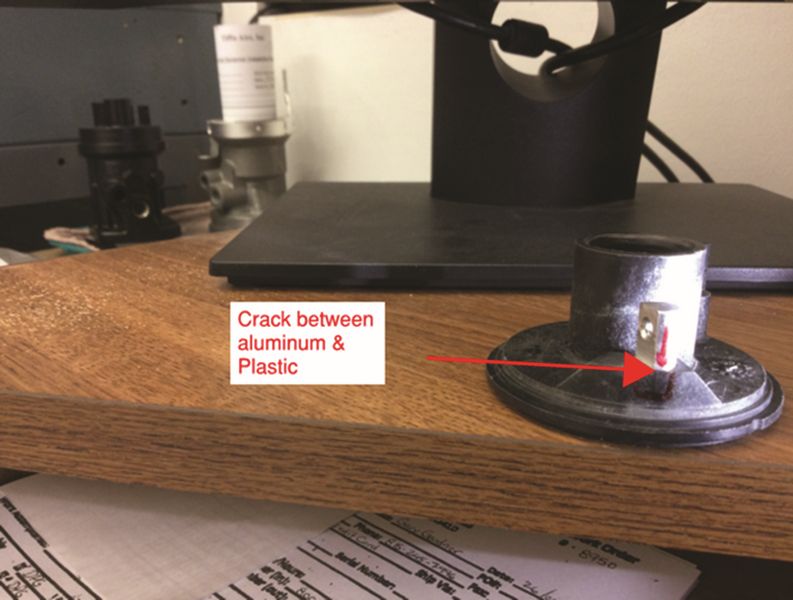
There Were Service Letters
The inspection of our governor identified the cause of our surging problem: A crack in the plastic governor cover where the aluminum post mounts (see picture above) for attaching the propeller control linkage. This crack allowed the post to deflect slightly when the linkage was fully extended at full throttle, causing the rpm surge. It turns out that McCauley issued Service Letters 2001-10 and 2001-10C to address this problem, requiring the replacement of the original plastic cover with an aluminum cover. Our governor overhaul included replacing the plastic cover with a new aluminum replacement ($250), complying with the Service Letters and solving our surging problem.
As owner/operators, we are responsible for operational safety, and reading Service Bulletins and Service letters speaks directly to that. I was not aware of this Service Letter or would not have waited a year to overhaul this governor. Additional searching for information on rpm surging found the plastic cover issue mentioned in our McCauley Governor Operator/Owner’s Manual Trouble Shooting section. See Page 102 in the March 13, 2013, Owner’s Manual, where our exact problem is pointed out:
The Owner’s Manual also recommends following the engine manufacturer’s transfer collar test for leakage. Before this quest for propeller and governor knowledge, I had not closely read the prop governor’s owner’s manual — you should check yours out as well.
Propeller Ground Ops
Methodology for propeller rpm cycling pre-takeoff is important because a) recommendations vary by propeller and engine brand, and b) improper cycling can cause an issue with crankshaft counterweight bushing wear, according to my highly regarded engine-overhaul shop manager. My brother had an otherwise-healthy IO-550 that began throwing alternator belts as an indicator of crankshaft counterweight bushing wear. He had no choice but to overhaul his engine at great expense and many months of down time.
So I questioned Lycoming and TCM tech support, as well as Hartzell and McCauley tech support, along with reading their published recommendations for pre-takeoff prop cycling. I also contacted a few IA mechanics, along with the predominant engine-overhaul shop here in the Chicago area asking two questions: What depth of rpm cycling is recommended pre-takeoff; and how many cycles should be performed?
I was interested to learn that answer is, “It depends.”
Prop Cycling History
The origins of propellor cycling operations began in the WWII era, when large radial engines used the “pressure dome” in the prop hub where engine oil is pumped, creating pressure to change propeller pitch and rpm. This is where the custom of deep rpm cycling, multiple times, became standard to confirm system operation. It was of particular concern at cold temperatures, when oil could be thick and not flow adequately until warmed up.
But nowadays we know the importance of preheating, so oil flow should not be our concern for prop cycling pre-takeoff. Oil-operated props on GA aircraft have passages to ensure the continuous flow of warm oil to the prop internals.
John Deakin, who developed Advanced Pilot Seminars with George Braly and Walter Atkinson, stated in his online article “Pelican’s Pearch #63: Where Should I Run My Engine?” (Part 1, from 2002), that deep cycling accomplishes nothing: “One short cycle of the prop with a 100 or 200 rpm drop is sufficient to indicate proper functioning, and further (or deeper) cycling accomplishes nothing, unless it’s very cold outside and the prop is sluggish.”
That is the first clear direction I found on the subject of pre-takeoff propeller rpm cycling for depth and number of cycles.
Lycoming vs. TCM
Engine-overhaul shops see the results of our operational practices and may have the best view to evaluate consequences. Our highly regarded overhaul-shop manager made it clear that for TCM engines, he preferred limiting prop cycling to no deeper than 200-300 rpm, and that limiting the number of cycles solely to confirm operation was important to protect crankshaft counterweight bushings.
Crankshaft counterweights oppose crankshaft lateral loads to reduce stress, and they move when rpm changes occur. Counterweight bushings come into play when there is movement of the counterweights, particularly toward the aft portion of the crankshaft, where the aft-most set of bushings tend to wear the most.
The shop manager also pointed out the exception to that rule is AD 77-05-04 for TCM 470 and 520 engines, where a 400 rpm drop is required three times for feathering propellers as an operational (transfer collar) check. If not performing this AD check, never cycle the propellor so deeply, he stated.
The shop manager’s final comment was eye-opening. He said that he’s never seen a Lycoming engine come in for overhaul due to worn counterweight bushings; however, it is not uncommon to see that for TCM engines, i.e. my brother’s 2021 engine overhaul.
When I questioned TCM tech support about prop-cycling recommendations, they deferred to the aircraft Pilot’s Operating Handbook (POH) and suggested limited cycling on the ground, as necessary. Regarding crankshaft counterweight bushing matters, TCM tech support mentioned Critical Service Bulletin (CSB) 09-11A where they found “crankshaft counterweight release … in high time IO-520 engines … that were operated at sustained cruise engine rpm of less than 2,300 rpm.”
The 2009-issued CSB goes on to say:
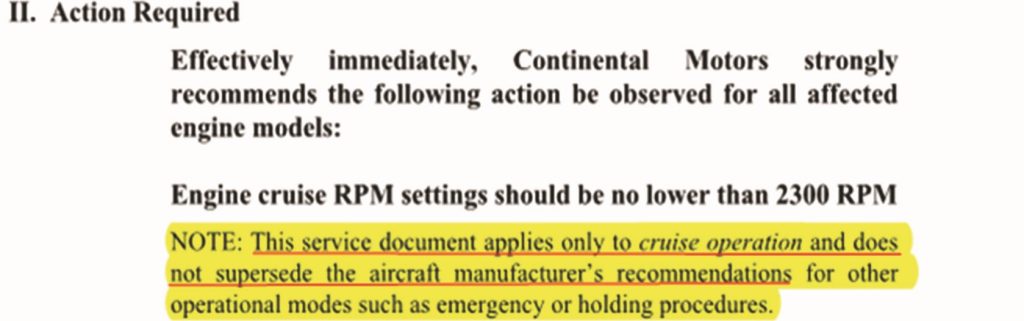
Keep in mind that these engines were exposed to severe conditions in cruise that do not equate to typical service operations or cycling on the ground. Still, I was not aware that cruise rpm could affect crankshaft counterweight bushing wear in TCM engines, but I should have been after many years of TCM ownership.
When questioning Lycoming tech support on this topic, they confirmed no published guidance on propeller cycling on the ground, or any documents related to crankshaft counterweight bushings. He deferred to the aircraft manufacturer’s POH and offered the suggestion to limit the number of ground cycles to no more than necessary, as well.
No POH Guidance
Keeping in mind the POHs of our legacy Cessnas were written 30 years ago or more, they are simply obsolete on certain subjects. I have observed occasional inaccuracies in the POH for our 182RG. As owner/operators, it critical for us to determine POH content correctness, particularly when our engine manufacturers and others defer to POH guidance.
The POH for our 1978 182RG shows the following in the Takeoff Checklist regarding prop cycling: “Propeller — CYCLE from high to low RPM; return to high RPM (full in).”
No POH guidance is mentioned for the low rpm figure or number of cycles pre-takeoff. As a knowledgeable owner, I will lean toward guidance from overhaul shops and engine or propeller manufacturers for pre-takeoff ground operations for my airplane.
The rest of this article including the advisement from McCauley and Hartzell can be seen only by paid members who are logged in.Have a website login already? Log in and start reading now.
Never created a website login before? Find your Customer Number (it’s on your mailing label) and register here.
Still have questions? Contact us here.