My Personal Experience With Hoses
I purchased a 1968 Cessna172I in October 2009 from an individual in Illinois. Annuals were completed in 2007 and 2008 by shops in Illinois. As an A&P, I personally completed the annual in March 2010. During the annual inspection, it was discovered that all engine and fuel hoses in the engine compartment were the original hoses, dated 1968. I was very surprised by this discovery. In reviewing the previous aircraft logs, there were no entries of hoses being replaced. This indicates that hoses may have been overlooked during required annual or 100-hour inspections. During the annual inspection on my aircraft in 2010, all hoses were replaced, along with some oil-soaked fire sleeves. Surprisingly, the original hoses were in service as oil and fuel lines, undamaged and still somewhat pliable.
Careful inspection and replacement of hoses, as necessary, will reduce the risk of an inflight emergency. This article is aimed toward pilots’ and owners’ understanding of uses and applications of aircraft hoses in GA aircraft with reciprocating engines. Aircraft with turbine engines are not included in this discussion.
Replacing Hoses
14 CFR, Part 43, Appendix A, Section (c), Preventive Maintenance (c21), (c22). Provides guidance for the owner/operator replacing hoses.
(c) 21 The owner/operator may replace any hose connection except hydraulic connections (brake hoses or hydraulic landing gear hoses).
(c) 22 The owner/operator may replace only prefabricated fuel lines.
Owner/Operator
The preventive maintenance described in (c 21) and (c 22) must be performed by the holder of at least a private pilot certificate issued under Part 61 who is the registered owner or co-owner of the aircraft and holds a certificate of competency for the aircraft.
Note: The written statements in FAA c21 and c22 above are a gray area and are not clearly defined. The statements are intended as guidance for an owner/operator. Any hose installed on an aircraft is a critical part of the aircraft and requires knowledge, experience, and special tools to deal with any issue with them. Replacing or repairing of any hose should be completed and signed off by a certificated A&P mechanic.
Log Entry
An aircraft logbook entry is required for all work completed on the aircraft.
The log entry includes:
- The date the work was completed.
- Description of the work completed.
- Description of the items repaired or replaced.
- Total airframe time when work was copleted.
- Signature of the person completing the work, including their FAA certificate number.
Types of Aircraft Hoses
Aircraft hoses are manufactured under the requirements of FAA TSO (Technical Standard Order), which is the Technical Standard for Materials, Processes, and Appliances used on all certified aircraft.
Aircraft hoses are covered under TSO C53a “Fuel and Oil System Hose Assemblies” and TSO C75 “Hydraulic Hose Assemblies.” Each TSO contains minimum performance standards for materials, parts, and processes for hose components used in aircraft.
Each TSO contains several types of hose, each of which has specific pressure ratings and operating temperatures.
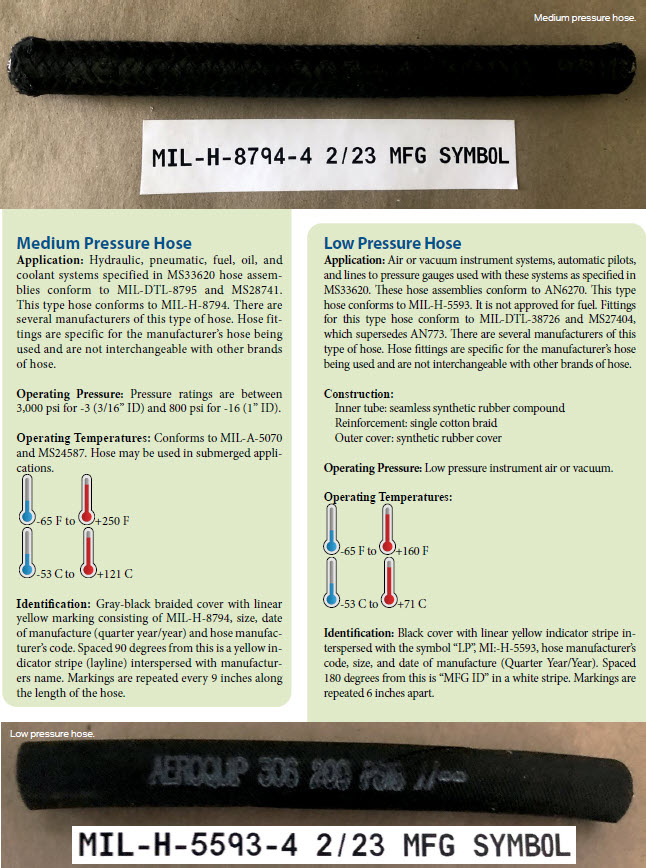
Determining Hose Life
The FAA information regarding hose life is very limited and does not address in-service life of elastomeric hose. The only reference to hose is shown below.
Reference FAA AC43.13 -1B “Acceptable Methods, Techniques, and Practices — Inspection and Repair, Paragraph 6-73 PG 6-16
6-73. Flexible Hose Assemblies.
- Inspect hose assemblies for chafing, weather-checking, hardening, discoloration, evidence of fungus, torn weather protective coatings or sleeves, and corrosion of fittings.
- Replace any defective, damaged, twisted, or bulging hoses.
General interpretation: Replace the hose if any damage is found.
Have a website login already? Log in and start reading now.
Never created a website login before? Find your Customer Number (it’s on your mailing label) and register here.
JOIN HERE
Still have questions? Contact us here.