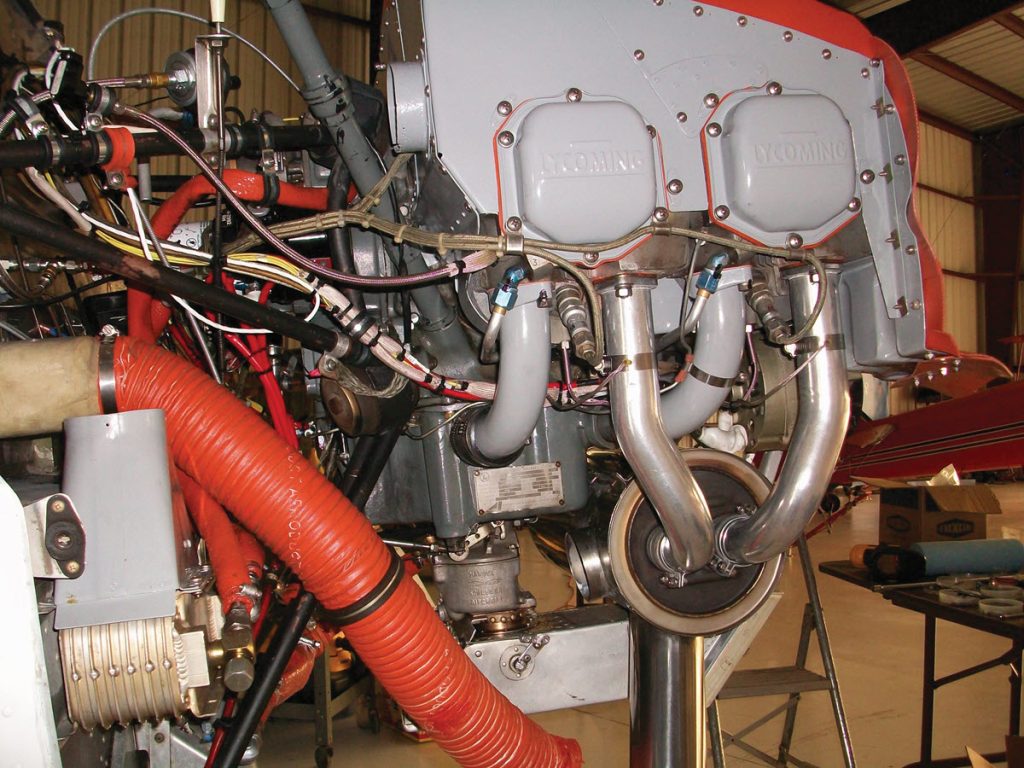
An Alternative to Paint
By John Bradley
Powder coating has become a booming industry and will be used for more and more applications as time goes on. Powder coating uses no solvents, has little or no effect on the environment, poses a very small health threat to the person applying it, and is very cheap compared to all current solvent-borne paint systems. As an example, one pound of powder costs $10 to $15 and will cover approximately 70 square feet with a 2 mil (0.002 inch) thickness, or about two sets of Lycoming baffles. Paint for the baffles would require one or two primer coats and two coats of color, which would be at least $150, depending what system was used. If an epoxy primer and a urethane color were used, the cost would be closer to $200.
The cost of powder coating is also less expensive due to the reduced amount of labor required. Most parts require only one coat, but if corrosion pitting is present, a powder primer can be applied, sanded with 240 grit, and a final color applied. The thickness of the powder primer coating is sufficient to fill fairly deep pits with one coat. A traditional paint primer would require several coats to fill the pits, with sanding in between coats.
Governmental Laws and Controls
Government regulations are having an increasing impact on the paints and solvents that can be used. These regulations are being enforced by federal government agencies, such as the Environmental Protection Agency (EPA), the Occupational Safety and Health Administration (OSHA), and the Department of Transportation (DOT). State agencies are also generating new and more stringent regulations. California, Massachusetts, New Jersey, and Pennsylvania are currently imposing new controls. Many counties and cities are also enforcing local regulations. Other countries, including Canada, Japan, and several European nations, are organizing enforcement agencies and creating new laws to control volatile organic compounds (VOCs), which include most solvents and reducers.
OSHA has imposed new regulations that deal with lowering exposure to chemicals, solvents, and curing agents. These new limitations on VOCs have a great impact on the entire coatings industry, including chemical companies, paint and coating manufacturers, and the shop that paints your aircraft.
New laws and controls are appearing on a regular basis and in all trade magazines that deal with painting and finishing processes. These new laws and regulations and tougher controls by enforcement agencies are currently affecting the solvents, primers, paints, processes, and procedures we use when restoring our classics. There is a significant research effort underway to lower the VOCs and increase the solids and pigments in paints. The new controls have also resulted in significant price increases for traditional paint products. The cost of powder coating has also increased. However, when factoring in the cost of the equipment necessary to meet the existing VOC regulations, powder coating remains the most economical coating process.
Keep It Clean
Powder coating materials are available in many types and colors. Our experience indicates that the best choices for aircraft applications are either epoxy or urethane coatings. These coatings offer greater durability and are available in an unlimited array of colors.
The coating, when cured, resists the impact of a 1-pound weight dropped from 13 feet without causing cracks in the coat ing. The weight has a .5-inch diameter ball affixed to the weight that impacts the test sample. The coating will even resist our “ape test,” which is to lay a coated sample on the floor and allow our largest technician to flog it with a mechanic’s ball-peen hammer. The coating is marred by the hammer blows but does not chip or crack. The ape test made a believer of me and proved the coating is almost indestructible.
Powder coatings can withstand a salt spray test for 1,000-plus hours with no apparent corrosion damage. Powder coating is the best protection for parts subjected to rock strikes or bug impacts, because it will not chip from rocks or during installation.
Powder coating has outstanding resistance to heat, oil, and fuel, making it the best choice for engine and engine compartment parts. Because the coating is cured at 400° F, it can be used on most engine components. However, it is not suitable for exhaust systems.
Experience has shown that the cost of powder coating is much less than the cost of conventional painting. A part to be painted requires the same surface preparation, including degreasing and sandblasting, as a part to be powder coated. The big difference is the cost of labor and materials for at least two coats of primer, with sanding in between coats, the time to wait for the primer to dry, and then the cost of applying the finish coat of paint. By comparison, the application and curing of powder coating on a complete set of Lycoming baffles requires, at most, one hour. The powder coating is completely cured after cooling and ready for assembly.
A painted part should not be handled or installed for at least one day to allow it to harden. Paint will fail under bolt, nut, or washer. Powder coating offers great durability and is, for the most part, unaffected by moisture, oil, fuel, and mineral-based hydraulic fluids (5606). Additionally, it is almost chip-proof.
Part Preparation
Preparing a part for powder coating is much the same as for conventional painting. Removal of all grease, oil, and other contaminates is necessary for good adhesion. Powder coating will “fisheye” just like paint if the parts aren’t clean. Our proven method for greasy or oily undercarriage parts is to disassemble them as far as possible and dip them in a “cold parts cleaner” similar to the old-style carburetor cleaner. The carb cleaner isn’t cheap, but it will do the job well. The parts will come out very clean after a good high-pressure water rinse.
We sandblast all parts with 50-80 (medium) grit media at a pressure of 80-90 psi for steel parts. Aluminum parts are sandblasted with no more than 50 psi.
Bead blasting is not recommended, because beads produce a round profile instead of a sharp profile. The sharp profile produced by the sand results in maximum mechanical bonding of the powder coating.
Steel parts are dipped in an iron phosphate solution at 140° F for two minutes. This process cleans residual blasting dust and places a thin surface coating that cleans residual blasting material and converts iron oxide (rust) to iron phosphate. This process results in additional adhesion of the powder coating during the curing process.
A slightly different process is used for parts with thinner material. The cleaning and sandblasting procedure is the same, but a good coat of powder is applied to the cold part. The part is then placed in the curing oven. The cured part is inspected after removal from the oven. If thin spots are discovered, the part is put back in the oven, reheated, and recoated while hot.
We have learned from experience that coating thickness can be a problem when coating parts that have areas that depend on tight fits or clearances. A nut will not start on a powder coated thread, and a bolt will not thread into a powder-coated hole. All threads and tapped holes have to be masked before powder coating. Silicone rubber plugs are available to mask threaded holes, and a special high-temperature Mylar tape is used to mask off gasket areas and externally threaded parts. The tape and silicone plugs remain on the part through the curing process and are easily removed after the part has cooled.
The Treatment and the Cure
Powder coating isn’t hard or brittle, and it will scratch. However, with reasonable care, parts can be assembled with no damage. Completed parts can be installed immediately after they are cool enough to handle. Paint requires dry time, and the paint will never be as durable as powder coating.
The powder used for coatings is finely ground resin with the consistency of talc. The powder is applied with an air-powered gun that applies a positive charge to the powder particles as they exit. The part is grounded and attracts the powder particles like a magnet. The particles go around corners, get into holes and crevices, and, when cured, completely seal the surface with no porosity.
The powder coating is cured for 10 to 15 minutes at 400° F. The powder actually melts, flows out on the surface of the part, and mechanically bonds to the surface. The bonding is so strong and the coating so durable that removing it is very difficult. Sandblasting takes forever, and even the strongest paint stripper will not affect it. Removing the coating requires immersion in a special hot alkaline bath for several days.
The 400° curing temperature for powder coating prevents its use on plastic parts or parts with rubber components. It is also not acceptable for exhaust manifolds or any part that will not tolerate temperatures above 400° F.
POWDER COATING BENEFITS
- Powder coating is an excellent choice for aircraft
applications. - Powder materials are non-toxic and inert.
- The cost of powder coating is well below the cost
of traditional painting methods. - Powder coating far exceeds the endurance of
traditional paints. - Powder coating has better corrosion and heat
resistance than paint. - Color selection is almost endless.
- Color selection includes high gloss, semi-gloss,
flat, gloss clear, semi-gloss clear, wrinkle, and
textured. - Coatings can be applied to anything that will
take the 400° curing temperature, including steel,
aluminum, cast iron, glass, ceramic, carbon fiber,
and some thermoplastics. - A powder-coated part will look just as good as a
painted one, will outlast several paint jobs and, at
the same time, help save our environment.
Small parts are placed in the curing oven and heated to 350° F for 10 to 20 minutes, depending on the size and thickness of the metal. An even coat of powder is then applied to the hot part. The powder melts upon contact with the hot surface, and thin spots can be spotted immediately and touched up. The part is then placed back in the oven for 10 to 15 minutes at 400° F for curing.
John Bradley is a retired mechanical engineer with 34 years’ experience designing oil field pressure equipment and subsea pressure vessels. He is an instrument-rated private pilot and owned and restored a 1968 Cessna 172I. Mr. Bradley is a certificated A&P mechanic with 10 years’ experience. Email jsmaviation@gmail.com